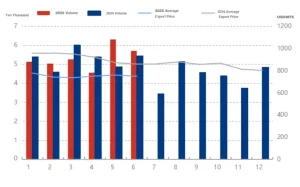
China Melamine Raw Material Price Analysis In JUN.2025
News China Melamine Raw Material Price Analysis In JUN.2025 1. China Melamine Raw Material Price Focus This Month In June 2025, melamine exports were 56,900
This article provides a detailed and comprehensive exploration of melamine production. It covers the properties of melamine, the raw materials involved, the complex production process and its various stages, quality control measures, environmental considerations and sustainable methods related to melamine production.
Melamine powder, an organic compound with the chemical formula C3H6N6, is a white crystalline powder.
It has high stability and a high melting point, which makes it suitable for a variety of applications.
Because of its stability and durability, it is commonly used in the production of kitchenware, laminates, adhesives, and flame retardants.
The primary raw material used in melamine production is urea, a white crystalline compound widely used.
Formaldehyde is another essential raw material. It is produced by the reaction of methanol and air in the presence of a catalyst.
The most common method for melamine production is the urea-based process. In this method, urea is thermally decomposed under high temperature and pressure conditions.
The chemical reaction can be generally expressed as:
6CO(NH₂)₂ → C₃N₆H₆ + 6NH₃ + 3CO₂
Urea molecules break down to form melamine, ammonia, and carbon dioxide.
Please read the specific process steps:Introduction Melamine Powder Manufacturing Process
Researchers are constantly exploring new methods for melamine production. Some of these approaches focus on improving energy efficiency, reducing environmental impact, or using alternative raw materials.
For example, studies are being conducted on biomass-derived feedstocks to produce melamine more sustainably, although these methods are still in the experimental-scale-scale stage.
In the Reactor
Maintaining the proper reaction temperature is crucial for the urea-based melamine production process. As mentioned earlier, the ideal temperature range is 350 – 400°C. If the temperature is too low, the conversion rate of urea to melamine will be low, resulting in low product yield.
On the other hand, if the temperature is too high, it may lead to side reactions, such as the formation of by-products that can contaminate the melamine product and reduce its quality. Advanced temperature control systems, such as thermocouples and feedback control loops, are often used to regulate precise temperature.
In Separation and Purification Steps
The temperature needs to be carefully controlled in the cooling and crystallization steps. For example, during crystallization, the cooling rate and the final crystallization temperature determine the crystal size and purity of the melamine. Too rapid cooling may result in tiny, irregular crystals containing impurities, while slow cooling may lead to low production efficiency.
In the Reactor
The high-pressure environment in the reactor is essential for the urea-based reaction. A pressure of around 7 – 10 MPa helps promote urea decomposition. Deviations from the proper pressure range can affect the reaction rate and product quality.
Pressure-relief systems need to be designed carefully to ensure safe operation. Any sudden or improper pressure release can lead to safety hazards and disrupt production.
In Separation Processes
Controlled pressure relief separates ammonia and carbon dioxide from the reaction mixture. This helps to efficiently separate the gaseous by-products while maintaining the integrity of the remaining product mixture.
The quality standards of melamine products are crucial for ensuring the final product’s safety, reliability, and highest quality.
The critical quality standards for melamine products include purity, colour, moisture content, and particle size distribution.
For most applications, the purity of melamine must be at least 99.8%.
Testing and inspection are critical stages in the production process of melamine.
Melamine products must comply with strict quality standards to ensure their safety and functionality.
The testing process includes checking melamine products’ physical and chemical properties, including their purity, colour, and moisture content. Inspect at different stages of production to detect any defects or irregularities in the product.
Quality control measures involve strict testing of raw materials before production, continuous monitoring of process parameters during production, and thorough product testing after production. Techniques such as chromatography and spectroscopy are used to analyze the purity of melamine.
Melamine powder production is energy-intensive, requiring significant electricity and fossil fuels. This poses a challenge in terms of environmental impact.
One of the significant environmental challenges in melamine production is the release of ammonia. During the production process, especially in the reaction and separation steps, ammonia is produced and can be emitted if not adequately controlled. Ammonia emissions can cause air pollution and adversely affect human health and the environment.
Advanced gas-handling systems, such as scrubbers and catalytic converters, capture and convert ammonia into less harmful substances to address this issue.
The production process also generates solid and liquid wastes. The solid waste may contain unreacted urea, by-products, and other impurities. Proper disposal and treatment of these wastes are necessary to prevent soil and water pollution.
Recycling and reusing some waste materials, such as recovering urea from solid waste for reuse in production, can help reduce the environmental impact and lower production costs.
Renewable energy sources, such as solar or wind power, are used to supply power to production facilities.
Water conservation measures are implemented to reduce water usage.
Closed-loop systems are developed to minimize waste and ensure that – products are reused or recycled.
CCUS is currently the only technological choice for achieving low-carbon utilization of fossil fuels, a necessary technical means for achieving large-scale greenhouse gas emissions reduction, a feasible technical solution for deep decarbonization of difficult-to-reduce industries such as steel, cement, non-ferrous metals, and chemical industries, and an essential component of the technology combination for achieving carbon neutrality goals.
As China leader melamine manufacturers, we respond to the call for “carbon neutrality” and have launched a 100000-ton CO2 CCUS project to save energy and reduce emissions, striving to achieve net zero emissions.
Melamine production is a complex but essential chemical manufacturing process. The choice of production method, proper control of process parameters, addressing environmental and quality challenges, and understanding the significance of melamine in various industries are all crucial aspects.
Continued research and development in melamine production are needed to improve efficiency, reduce environmental impact, and meet the growing demand for high-quality melamine in different applications.
News China Melamine Raw Material Price Analysis In JUN.2025 1. China Melamine Raw Material Price Focus This Month In June 2025, melamine exports were 56,900
News China Melamine Analysis In May.2025 1. China Melamine Powder Export date In May 2025, melamine powder exports reached 63,000 tons, up 38.16% from the
Tech Blog How Melamine Molding Compound Powder Is Revolutionizing Industrial and Household Products Melamine molding compound powder (MMC powder)-thermosetting polymers synthesized from melamine formaldehyde (MF)
JINGJIANG MELAMINE POWDER
© JINJIANG MELAMINE