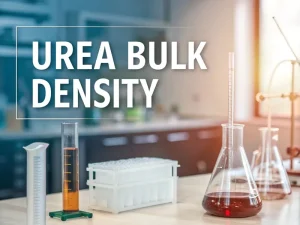
Urea Bulk Density
Tech Blog urea bulk density Urea – whether used as a high nitrogen fertilizer, industrial production raw material, or a component of diesel exhaust fluid
Urea synthesis is based on the Bosch Meiser process, which involves the reaction of ammonia (NH3) with carbon dioxide (CO₂) under high pressure. Urea is the most widely used nitrogen fertilizer, and it is also widely used in industry, directly affecting global fertilizer and various industries with an annual output value of 60 billion US dollars.
This article delves into the chemical processes and reaction mechanisms behind the ammonia to urea reaction.
The synthesis of urea from ammonia and carbon dioxide is divided into two different stages, each with specific thermodynamic requirements:
Ammonia and carbon monoxide react at high pressure and moderate temperature to form ammonium carbamate, which is an unstable intermediate:
2NH3+CO2⇌NH4COONH2
Ammonium carbamate decomposes into urea and water under reduced pressure and high temperature:
NH4COONH2⇌CO(NH2)2+H2O
Solubility challenge: Ammonium carbamate has a high solubility in liquid ammonia, while urea has limited solubility, which helps with product separation.
Catalyst function: No specific catalyst is required because the reaction proceeds fully under pressure, although impurities such as iron and nickel can reduce product quality.
Ammonia production:
Haber Bosch process: N ₂ (air)+3H ₂ (natural gas/coal) → 2NH ∝, requiring~3.5-4.5 GJ/ton of ammonia.
CO₂ source:
Capture from industrial flue gas (such as hydrogen production, cement kilns) or by-products of ethanol fermentation.
Nitrogen fertilizer: The high nitrogen content (46.65% by mass) and water solubility of urea make it the preferred nutrient for crops worldwide, approximately 180 million tons are produced annually, accounting for 30-40% of global cereal production.
Slow-release formula: Coated urea particles (such as sulfur-containing or polymer) can minimize ammonia volatilization and increase nutrient utilization efficiency by 10-15%.
Selective Catalytic Reduction (SCR): Urea-based AdBlue solution (32.5% urea) reduces nitrogen oxide emissions from diesel trucks through NH.
Formaldehyde resin: a cross-linked polymer used for wood adhesives, particleboard, and molded plastics, with an annual output of over 5 million tons.
Medical and pharmaceutical applications
Dialysis and renal function: The role of urea as a nitrogen waste enables blood urea nitrogen (BUN) testing to be used for kidney health assessment.
Local skin care: Urea cream (10-40%) utilizes the hygroscopicity and keratolytic properties of this compound to moisturize the skin and remove dead cells.
The anaerobic digestion of feces or food waste produces biogas (CH₄), which is sent to the carbon-neutral Haber Bosch process for ammonia production.
By utilizing renewable electricity to decompose water into hydrogen gas and combining it with nitrogen gas through the solid-state Haber process, CO₂ emissions can be reduced by 80-90%.
EU initiative and other projects are examples of the direct synthesis of urea and green ammonia from captured CO₂. As leader China urea factory, Jinjiang actively responds to the call for environmental protection and has already put into operation a 100,000-ton CO2 CCUS project.
The ammonia to urea reaction has undergone a century of development, converting abundant nitrogen and carbon resources into molecules that sustain the global food system and drive industrial progress. Although current processes rely on fossil fuels, continuous innovation in renewable ammonia production, carbon capture, and efficient reaction engineering is expected to make urea synthesis more sustainable.
As we face the challenges of climate change and food security, the ability to convert ammonia into urea remains at the core of balancing human demand and environmental management, both now and in the future.
Tech Blog urea bulk density Urea – whether used as a high nitrogen fertilizer, industrial production raw material, or a component of diesel exhaust fluid
Tech Blog urea for BS6-Everything you need to know about DEF If you have recently purchased a new BS6 diesel vehicle in India, whether it
Tech Blog DEF urea concentration If you own a modern diesel car, the “DEF” or “AdBlue” indicator lights on the dashboard are definitely familiar to
JINGJIANG MELAMINE POWDER
© JINJIANG MELAMINE