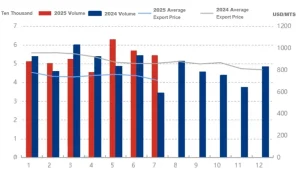
China Melamine Market News In July.2025
News China Melamine Market News In July.2025 1. China Melamine Market News Focus This Month In July 2025, melamine powder exports were 54,600 tons, down
The density of melamine is 1.573g/cm ³, measured at 16 ℃. As mentioned above, this density value is an important physical property of melamine and can serve as a fundamental reference for understanding its behavior and applications in different industries.
It is worth noting that the actual density may vary slightly due to factors such as the purity of melamine, the manufacturing process, and any impurities or additives that may exist.
The bulk density of melamine typically falls within the 700 – 900 kg/m³ range. However, some sources may provide slightly different values:
Some industrial-grade melamine is specified to have a bulk density of 800 – 1100 gm/ltr.
The Melamine (High Purity) from Filo Chemical reportedly has a bulk density of 0.3 ± 0.01 g/ml.
Melamine has a relatively moderate density. Compared to some common organic substances, its density of about 1.574 g/cm³ is relatively high. For example, the density of water is 1 g/cm³, and melamine is denser than water. However, compared to many metals and some inorganic compounds with high densities, such as lead with a density of 11.34 g/cm³ or mercury with a density of 13.534 g/cm³, melamine is not extremely dense.
In the context of its applications, melamine’s density is neither overly high nor overly low, which endows it with suitable physical properties for many uses, such as in the production of melamine resins, where its density contributes to the formation of products with specific mechanical properties.
Principle: The specific gravity method is a commonly used method for measuring the density of melamine powder.
Use a specific gravity bottle, a precise calibration container with a known volume. Firstly, weigh the particular gravity of the empty bottle. Then, fill it with melamine powder and measure the mass of the specific gravity bottle filled with it. Next, remove the powder and fill a particular bottle of gravity with a known density of the liquid (usually a nonreactive and low-viscosity liquid such as ethanol). By measuring the mass of a volumetric flask filled with liquid, the volume difference between the liquid with and without powder can be used to calculate the volume of the powder. Then, the density of melamine powder is determined by dividing the mass of the powder by its volume.
Accuracy: The specific gravity method provides a high-precision measurement of the true density of melamine powder. It considers the powder particles’ volume and does not include gaps between particles. This method is particularly useful when industries such as high-performance plastic manufacturing require precise density values for research or quality control.
Program: Bulk density is another important parameter related to the density of melamine powder. Pour a known powder volume into a container to measure the bulk density. Then, measure the mass of the powder in the container. The bulk density is calculated by dividing the powder’s mass by the container’s volume. This measurement has different standard methods, such as the compaction density method. Before measuring the mass, the container is compacted several times to make the powder more consistent.
Meaning: Bulk density indicates the behavior of powder during handling, storage, and transportation. Understanding the bulk density of melamine powder is crucial for designing appropriate storage bins and handling equipment and estimating the amount of powder that can be stored or transported within a given volume.
Particle size: Smaller melamine powder particles often have higher packing density. When the particles are small, they can bind more tightly together, reducing the amount of air space between them. For example, compared to coarser ground powders with larger particles, finely ground melamine powders with an average particle size of a few micrometers may have a higher density. This is because smaller particles can form a more compact arrangement, resulting in higher unit volume mass.
Particle shape: Irregular-shaped particles may have lower packing density compared to spherical particles. Due to their symmetry, spherical particles can be stacked more effectively. For melamine powder, if the manufacturing process results in a large number of irregularly shaped particles, the overall density of the powder may decrease because the particles cannot be tightly stacked together, leaving more gaps between them.
Synthesis conditions: The synthesis conditions of melamine will affect its density. For example, the reaction temperature and pressure during the production of melamine from urea can affect the resulting powder’s crystal structure and particle characteristics. Higher reaction temperatures may lead to the formation of larger and more porous crystals, resulting in a decrease in powder density. On the other hand, optimized reaction conditions can produce denser and more uniform powders.
Drying and grinding Processes: The drying and grinding processes also play an important role. If the drying process is too fast, it may lead to the formation of hollow or porous particles, reducing density. Similarly, the grinding process can affect the particle size and shape of the powder, as well as the bulk density. Excessive grinding may produce many small particles, which can clump together and affect the overall density.
News China Melamine Market News In July.2025 1. China Melamine Market News Focus This Month In July 2025, melamine powder exports were 54,600 tons, down
News China Melamine Raw Material Price Analysis In JUN.2025 1. China Melamine Raw Material Price Focus This Month In June 2025, melamine exports were 56,900
News China Melamine Analysis In May.2025 1. China Melamine Powder Export date In May 2025, melamine powder exports reached 63,000 tons, up 38.16% from the
JINGJIANG MELAMINE POWDER
© JINJIANG MELAMINE